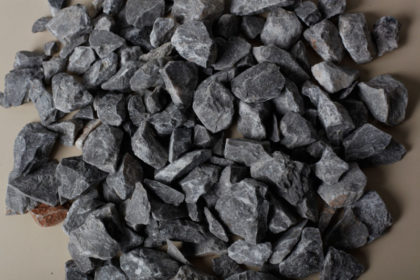
Aggregate; It is the name given to inorganic materials with different mineral structures such as sand, gravel, crushed stone, which are used with cement and water in the production of concrete mortar.
It is the most important component of the Asphalt Plant Used in Asphalt Production.
Physical characteristics of aggregates:
Maximum grain size and gradation: Maximum grain size and gradation is determined according to the layer it will use.
Whether it is clean or not: Aggregates should not contain plant wastes, soft materials, clay lumps and extraneous matter.
Grain shape: The grain shape of the aggregate affects workability, compressibility and stability. The use of angular, broken grains is preferred.

agrega-1
Surface structure of grains: In bituminous mixtures, they affect the load carrying capacity. Aggregates with very rough surfaces show high resistance against shear tensiles.

agrega-2
Porosity: It affects the percentage of bitumen in the mix. Mixture aggregates require some porosity to achieve aggregate bitumen adhesion.

agrega-3
Robustness: Aggregates to be used in bituminous coatings can be resistant to breakage, decomposition by water and frost.
Ability to be coated with bitumen: Aggregates used in bituminous coatings should not show peeling with the effect of water when coated with bitumen. Aggregates with low peel strength can be used by adding special additives to bitumen.
Aggregate used in asphalt road mix are hard minerals selected by classification according to their physical characteristics and dimensions depending on the mix design. These minerals can be of natural origin, such as crushed stone, gravel, or artificial, such as black cinder. Natural aggregates; They are aggregates taken from river beds, lake edges, quarries and which have not been processed except crushing, washing and classification. Artificial aggregates; They are aggregates that are produced for decorative purposes or by determining their properties or that can be produced as a by-product of any sector.
Aggregates are divided into 3 according to their weight.
Normal aggregates: These are aggregates with specific gravity between 2.0 and 3.0 kg/l. Sand and gravel can be examples of these aggregates.
Light aggregates: These are aggregates with a specific gravity of less than 2.5 kg/l. Lightweight aggregates, which generally have a porous structure, provide sound and heat insulation properties in the concrete where it is used. Lightweight aggregates have low resistance to pressure, impact and abrasion. Water absorption and void ratios are high. Pumice, , clay and perlite can be given as examples for this type of aggregate.
Heavy aggregates: These are aggregates with a specific gravity above 3.0 kg/l. It is used to obtain heavy concrete. Barite, magnetite and limonite can be given as examples of heavy aggregates, which are more expensive in terms of both material and workmanship compared to normal aggregates.
Thinnish and washable materials, organic substances and light substances damage aggregates because they damage the solidification or hardening of concrete, reduce its strength or compactness, and jeopardize its protection against corrosion. Therefore, the aggregates should be strong, should not be eroded, and should not be softened and dispersed by the effect of water. In addition, the shape and texture of the aggregate particles should be perfect, and they should be suitable for the purpose and standards in terms of size.